A Doctor Blade Coater is a widely used coating technology in industries such as printing, paper manufacturing, electronics, and materials science. It is employed to apply a uniform layer of liquid, paste, or slurry onto a substrate (such as paper, film, metal, or glass). The doctor blade coater ensures precise thickness control and high-quality coatings by regulating the amount of material applied.
---
●What is a Doctor Blade Coater?
A doctor blade coater consists of a sharp-edged blade (the "doctor blade") that regulates the thickness of the coating material as it is spread onto the moving substrate. The blade scrapes off excess material, leaving behind a controlled and uniform layer. This method is particularly effective for applications requiring consistent thickness and smooth surface finishes.
---
●Key Components of a Doctor Blade Coater
1. Doctor Blade:
- A thin, flat blade made of materials like stainless steel, ceramic, or polymer.
- Positioned at a specific angle (called the "blade angle") relative to the substrate.
- Controls the thickness of the coating by scraping off excess material.
2. Coating Reservoir:
- Holds the coating material (e.g., ink, adhesive, paint, or slurry) before it is applied to the substrate.
3. Substrate Transport System:
- Moves the substrate (e.g., paper, plastic film, or metal foil) beneath the doctor blade at a controlled speed.
4. Blade Holder:
- Secures the doctor blade in place and adjusts its position and angle.
5. Pressure Adjustment Mechanism:
- Allows fine-tuning of the pressure exerted by the blade on the substrate to achieve the desired coating thickness.
---
●How Does a Doctor Blade Coater Work?
1. Material Application:
- The coating material is applied to the substrate either by flooding the surface or using a roller to distribute it evenly.
2. Blade Action:
- As the substrate moves beneath the doctor blade, the blade scrapes off excess material, leaving a uniform layer of the desired thickness.
3. Thickness Control:
- The thickness of the coating is determined by factors such as:
- Blade angle
- Blade pressure
- Substrate speed
- Viscosity of the coating material
4. Drying/Curing:
- After coating, the substrate passes through a drying or curing system to solidify the applied layer.
---
●Advantages of Doctor Blade Coaters
1. Uniform Coating:
- Provides precise control over coating thickness, ensuring consistency across large surfaces.
2. Versatility:
- Suitable for a wide range of materials, including liquids, pastes, slurries, and viscous fluids.
3. Cost-Effective:
- Minimizes waste by removing excess material during the coating process.
4. High Throughput:
- Efficient for continuous production processes, especially in industries like paper and packaging.
5. Customizable:
- Blade angle, pressure, and substrate speed can be adjusted to meet specific application requirements.
---
●Applications of Doctor Blade Coaters
1. Printing Industry:
- Used for applying ink onto paper or film in flexographic and gravure printing processes.
2. Paper Manufacturing:
- Coating papers with materials like starch, clay, or polymers to enhance properties such as gloss, water resistance, or printability.
3. Electronics:
- Applying conductive inks, adhesives, or dielectric materials onto substrates for printed circuit boards (PCBs) or flexible electronics.
4. Energy Storage:
- Coating electrodes with active materials (e.g., lithium-ion battery slurries) during the manufacturing of batteries and supercapacitors.
5. Pharmaceuticals:
- Coating tablets or films with protective or functional layers.
6. Construction Materials:
- Applying adhesives, sealants, or coatings onto building materials like laminates or panels.
---
●Factors Affecting Coating Quality
1. Blade Material:
- The choice of blade material affects wear resistance, flexibility, and performance.
2. Blade Angle:
- Adjusting the angle influences the coating thickness and uniformity.
3. Blade Pressure:
- Higher pressure reduces coating thickness but may increase wear on the blade.
4. Substrate Speed:
- Faster speeds reduce dwell time, affecting coating quality and thickness.
5. Coating Material Properties:
- Viscosity, surface tension, and rheology of the material impact how it spreads and adheres to the substrate.
---
●Challenges in Using Doctor Blade Coaters
1. Wear and Tear:
- Continuous use can cause wear on the blade edge, leading to uneven coatings.
2. Air Bubbles:
- Trapped air bubbles in the coating material can result in defects.
3. Edge Effects:
- Uneven coating near the edges of the substrate due to flow dynamics.
4. Material Adhesion:
- Poor adhesion of the coating material to the substrate can compromise performance.
5. Viscosity Control:
- Variations in material viscosity can affect coating uniformity.
---
●Maintenance of Doctor Blade Coaters
1. Regular Cleaning:
- Prevents residue buildup on the blade and substrate.
2. Blade Inspection:
- Checks for wear, damage, or dullness of the blade edge.
3. Calibration:
- Ensures proper alignment and pressure settings for consistent results.
4. Lubrication:
- Reduces friction between the blade and substrate where applicable.
Tape Casting Coater
---
●Innovations in Doctor Blade Coating Technology
1. Advanced Blade Materials:
- Development of harder, more durable blade materials to extend service life.
2. Automated Systems:
- Integration of sensors and feedback systems for real-time monitoring and adjustment of coating parameters.
3. Surface Treatments:
- Coatings on blades to improve wear resistance and reduce material sticking.
4. Digital Control:
- Use of computer-controlled systems for precise adjustment of blade angle, pressure, and substrate speed.
---
●Conclusion
Doctor blade coaters are indispensable tools for achieving uniform and high-quality coatings in various industries. Their ability to regulate coating thickness precisely makes them ideal for applications ranging from paper manufacturing to advanced electronics. By addressing challenges such as wear and viscosity control, and adopting innovative technologies, manufacturers can further enhance the efficiency and reliability of doctor blade coating processes.
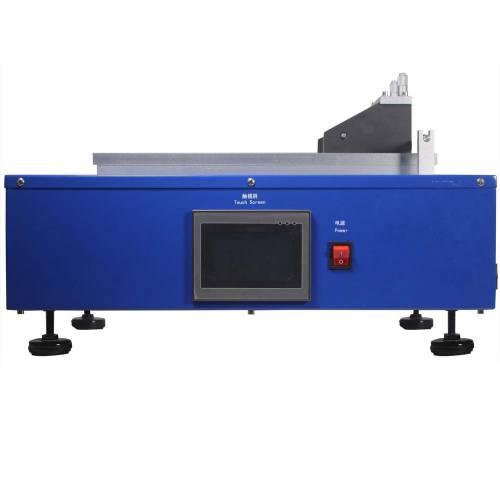