Lithium Cell Production Plant: Building the Heart of Modern Energy Storage
A lithium cell production plant is a specialized facility designed to manufacture lithium-ion cells, the core components of modern rechargeable batteries. These cells power a wide range of devices, from consumer electronics to electric vehicles (EVs) and renewable energy storage systems. The production process involves a series of precise and controlled steps to ensure high-quality, efficient, and safe lithium-ion cells.
This article explores the critical components, processes, and equipment involved in a Cylindrical Cell Assembly Plant.
● Key Components of a Lithium Cell Production Plant
1. Raw Material Processing Area
- Materials like cathode, anode, separator, and electrolyte are prepared for cell assembly.
- Includes mixers, blenders, and coating equipment to create electrode slurries.
2. Electrode Fabrication Zone
- Coating Machines: Apply slurry to current collectors (aluminum for cathodes, copper for anodes).
- Drying Units: Remove solvent from the coated electrodes.
- Calendaring Machines: Compress electrodes to achieve uniform thickness and density.
3. Cell Assembly Line
- Electrode Cutting: Precisely cuts electrodes into desired shapes.
- Stacking or Winding Machines: Assemble electrodes and separators into cell structures (pouch, cylindrical, or prismatic).
- Tab Welding: Welds current collector tabs for electrical connectivity.
4. Electrolyte Filling Station
- Injects a precise amount of liquid electrolyte into the cells to enable ion conduction.
5. Sealing and Packaging
- For pouch cells: Heat sealing ensures airtight encapsulation.
- For cylindrical or prismatic cells: Metal casings are crimped and sealed.
6. Formation and Testing Area
- Cells undergo initial charging (formation) to stabilize the electrochemical reactions.
- Comprehensive quality checks, including capacity, voltage, and safety tests.
7. Dry Room and Clean Room Environments
- To prevent contamination, critical production stages are conducted in dry and clean room conditions, ensuring moisture and particulate control.
8. Quality Control and Analysis
- Advanced testing equipment evaluates each cell's performance, durability, and safety.
- Includes x-ray inspection, impedance analysis, and thermal testing.
● Core Processes in Lithium Cell Production
1. Electrode Manufacturing
- Cathodes typically use materials like lithium nickel manganese cobalt oxide (NMC) or lithium iron phosphate (LFP).
- Anodes are commonly made from graphite.
- Both materials are mixed into slurries and coated onto current collectors.
2. Cell Assembly
- Includes stacking or winding electrodes with separators to form the basic cell structure.
- Conducted in a controlled environment to prevent contamination and moisture absorption.
3. Electrolyte Filling
- High precision is required to inject the exact amount of electrolyte, which is crucial for cell performance and safety.
4. Sealing and Encapsulation
- Ensures the cell is airtight, preventing leakage or contamination.
5. Formation and Aging
- Cells are charged and discharged multiple times to activate the internal chemistry.
- Aging tests identify potential issues before deployment.
6. Testing and Packaging
- After passing quality checks, cells are labeled, packaged, and prepared for distribution.
● Essential Equipment in a Lithium Cell Production Plant
1. Mixers and Slurry Preparation Units
- Mix electrode materials for consistent quality.
2. Coating Machines
- Apply uniform layers of active material onto current collectors.
3. Roll Presses (Calendaring Machines)
- Compress electrodes to the desired density.
4. Cutting Machines
- Precision cutting ensures consistent electrode dimensions.
5. Stacking/Winding Machines
- Assemble electrodes into the desired configuration.
6. Electrolyte Filling Machines
- Precisely inject electrolytes into cells.
7. Sealing Machines
- Heat seal or crimp cells for airtight encapsulation.
8. Formation Chargers
- Charge and discharge cells during the formation process.
9. Quality Testing Equipment
- Test cells for voltage, capacity, internal resistance, and safety.
10. Environmental Control Systems
- Maintain optimal conditions in dry and clean rooms.
● Advantages of a Lithium Cell Production Plant
1. Scalability
- Plants can be designed for small-scale pilot production or large-scale manufacturing to meet global demand.
2. Customization
- Flexible processes allow for the production of various cell types (pouch, cylindrical, or prismatic).
3. Quality Assurance
- Advanced testing and quality control ensure reliable and safe cells.
4. Sustainability
- With proper recycling systems, waste from the production process can be minimized, supporting a circular economy.
● Challenges in Lithium Cell Manufacturing
1. High Initial Investment
- Setting up a production plant requires significant capital for equipment, facility design, and skilled labor.
2. Material Sourcing
- Dependence on critical materials like lithium, cobalt, and nickel can lead to supply chain vulnerabilities.
3. Environmental Concerns
- Managing waste and emissions from production is critical to meet regulatory standards.
4. Technological Complexity
- Ensuring consistency and quality in mass production requires advanced technology and expertise.
● Applications of Lithium Cells
1. Electric Vehicles (EVs)
- Powering EVs is one of the primary applications, with a focus on high energy density and fast charging.
2. Consumer Electronics
- Used in smartphones, laptops, and wearable devices due to their lightweight and long-lasting power.
3. Energy Storage Systems
- Store renewable energy from solar and wind for grid or off-grid use.
4. Aerospace and Defense
- Reliable energy sources for drones, satellites, and other aerospace applications.
● Conclusion
A lithium cell production plant is a critical component of the global shift toward renewable energy and electrification. By combining precision manufacturing processes with advanced technology, these plants produce high-performance lithium-ion cells that power the devices and systems shaping our future. Despite challenges such as high costs and material sourcing, continuous innovation in production methods and materials is paving the way for more efficient, sustainable, and accessible energy solutions.
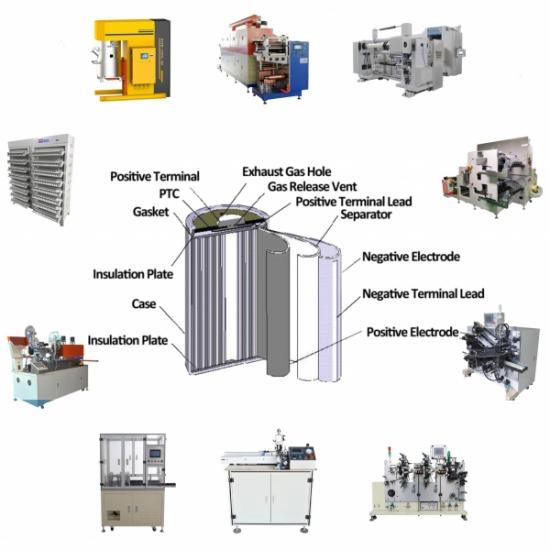